Hands-On Support From Hoover’s Own Team
Good preventative maintenance agreements - ones that deliver more than words - are hard to find in our industry.
When they offer them at all, competing pump station manufacturers tend to outsource to third parties that are ill-equipped to anticipate emergent problems, and incentivized to sell replacement parts instead of prolonging the lifespan of components you’ve already paid for.
We Never Outsource Maintenance Or Repair Work
Hoover employs its own technicians to carry out all routine maintenance, service and repair work because they’re intimately familiar with our pump station technology, and have the experience required to spot problems or opportunities to increase efficiency that other, less qualified technicians would miss.
Our hands-on approach is supported by Hoover's own Flowguard software that allows us to look at every aspect of your pump station operation for at least the last year. It's a combination that enables us to deliver proactive maintenance that guarantees far better results than any number of drive-bys or fixed number of visits each year.
We're not motivated to sell replacement parts; for us, preventative maintenance for our pump stations means getting ahead of breakages and costly repairs for customers.
We know the biggest benefit to our bottom line comes from a reputation for supplying top of the line equipment that can go the distance and the regular oversight and maintenance required to keep a pump station running smoothly and reliably.
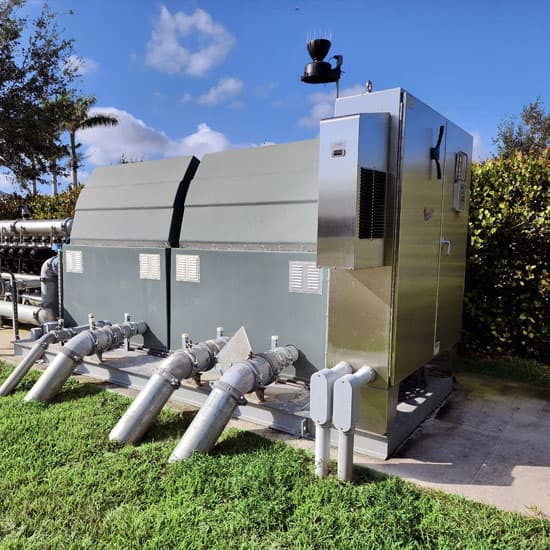
